Read fuller coverage of this story in Chinese
It’s the height of summer in the southern Chinese city of Guangzhou, and the heat is relentless. The sun beats down on the streets, evaporating the rainwater and creating stifling levels of humidity.
In urban villages -- slums, essentially -- around Haizhu district, where tightly packed buildings block the sunlight, the ground stays wet longer, making the narrow alleys slightly cooler than the main roads.
Inside the buildings, migrant workers from across China labor in garment factories to produce clothing for super-cheap fast-fashion brands, mostly SHEIN, which has been making inroads into American and European markets.
They work 12-hour shifts with minimal rest, yet they are highly skilled in producing whole garments from cutting to finishing.
Everything they need — jobs, housing, food, and essentials — is only a 10-minute electric scooter ride away. Yet their employment is often short-term and informal, and they’re not included in local government welfare or social security systems.
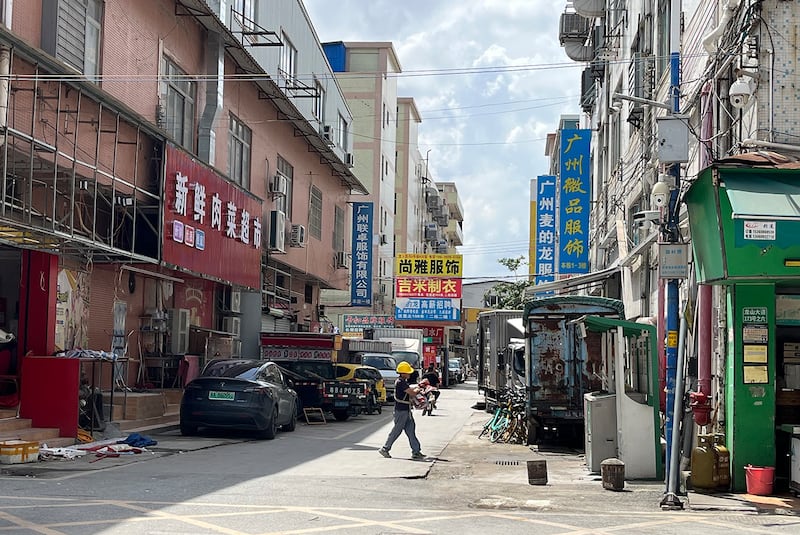
Their sought-after skills drive SHEIN’s profits, yet they’re insecurely employed and could be laid off or relocated elsewhere in China at the drop of a hat, should the company want to cut costs.
These workers haven’t always meekly accepted their fate.
In September 2022, the Kanglu garment district of Haizhu saw a major protest against grueling lockdowns under the ruling Communist Party’s zero-COVID policy, which ended later in the same year following nationwide protests.
Media coverage of those protests focused on the poor working conditions, grueling hours and insecurity in the garment factories of Kanglu, all of which were made worse by the lockdowns and quarantine measures.
Guangzhou’s garment-making district
Zhicun and Licun are both urban villages with high concentrations of garment factories near the Dashi Metro, a major subway station in Guangzhou.
Zhicun, near the entrance to Chimelong Safari Park, is undergoing heavy roadwork, making it hard to get around. Residential rents have risen recently; one local woman told Wainao that she paid 900 yuan (US$123) a month for a single room, describing it as “daylight robbery.”
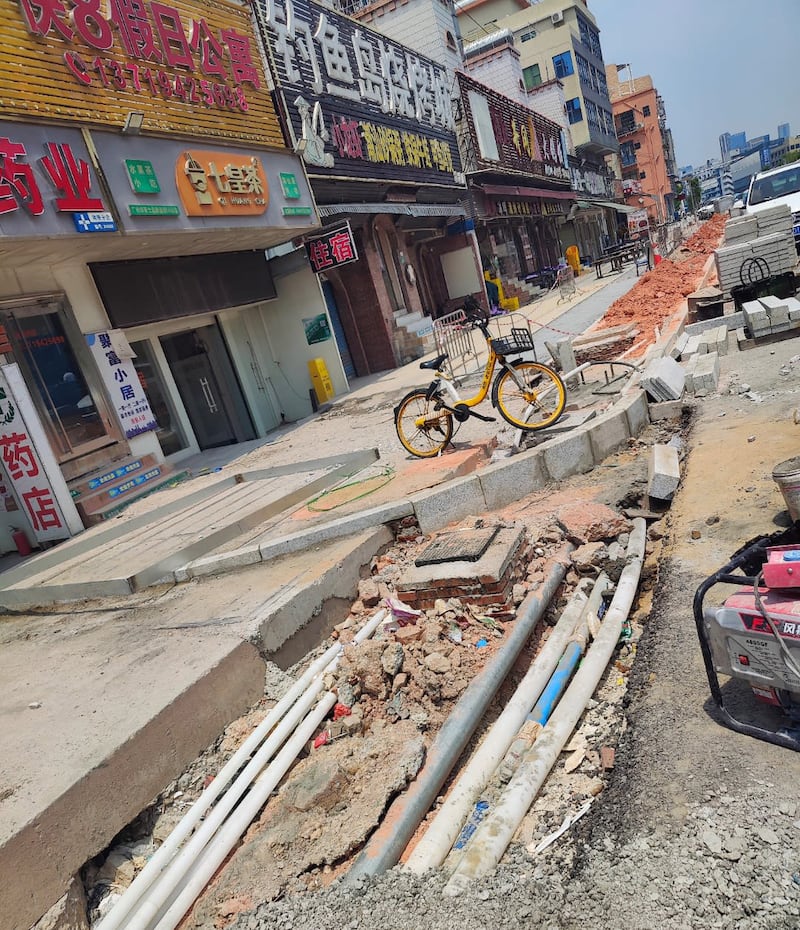
Licun is busier and cheaper, with crowded streets and shops. It’s not hard to find a meal costing less than 15 yuan (US$2), while rents range from 350-500 yuan (US$48-68) for a single room.
Garment factories in these slums take two forms: small workshops on the ground floors of three-story houses, where wide entrances make it easy to load and unload goods; mid-sized factories in village industrial parks, typically occupying one or two floors and employing dozens to 100 workers.
Some of the more formal factories have front desks and entry controls. In both villages, the smaller workshops are more prevalent, often lining the narrow alleys, with workers sitting outside folding finished garments into plastic packaging.
Larger garment factories on industrial parks typically offer dormitories for workers.
Very few of the factories, large or small, have air-conditioning in temperatures that routinely top 30 degrees Celsius (86 F) during summer.
RELATED STORIES
WAINAO: The delivery riders of the pandemic
INTERVIEWS: ‘I can’t even afford to eat any more’
INTERVIEWS: ‘I don’t know how I’m going to survive this winter.’
In the smaller factories, the line between worker and owner is sometimes blurred. The low capital requirements allow experienced garment workers with savings and connections to start their own businesses. It’s common for small factory owners to work alongside their employees.
S., an experienced overlock machine operator who like most interviewed didn’t want to be identified for fear of getting in trouble, has worked in the industry for more than 20 years.
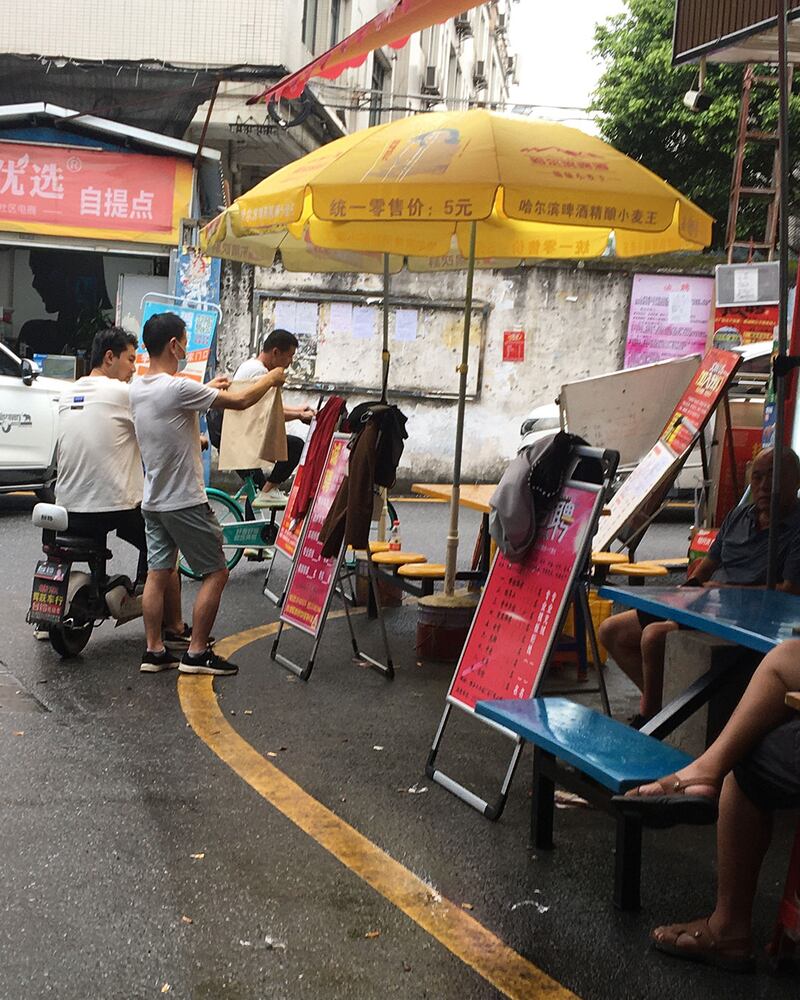
He spent a year at a Licun factory called PX after closing his own factory in Panyu. Since having children, he has prioritized flexibility over entrepreneurship, and takes time off when needed.
But he has never paid into any kind of social insurance, meaning that he can’t get medical treatment for his chronic back pain at public hospitals in Guangzhou. He must wait until he goes back to his hometown in the eastern province of Shandong.
A skilled yet precarious workforce
Finding a job in the garment industry isn’t easy, despite the large number of recruitment ads plastered in public places.
While bigger factories have assembly lines in which a worker will carry out a single part of the garment’s production, the smaller factories need workers who can make whole garments from scratch.
“If you don’t have that experience, no one will hire you,” S. told WHYNOT.
These workers need to be able to cut, stitch, overlock, inspect for quality and finish garments.
Precision and speed are essential, and factories are expected to turn out clothing in small batches with a fast turnaround time, a model that has powered SHEIN’s commercial success.
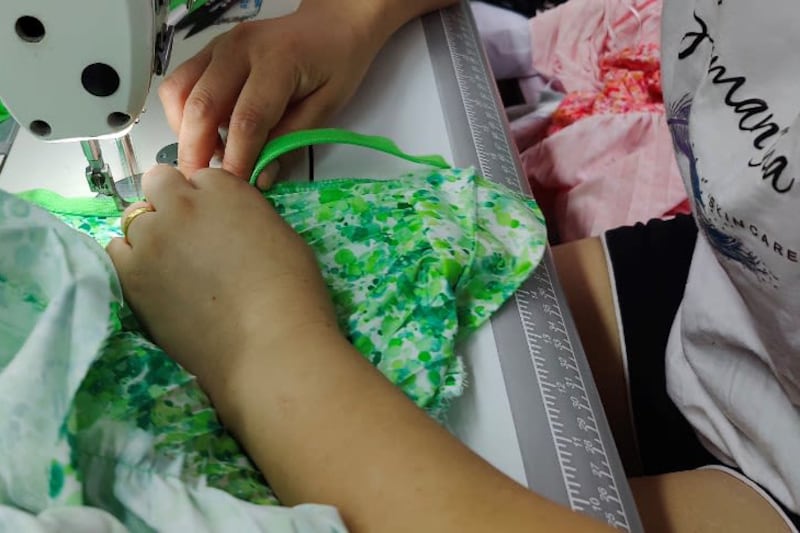
There are few routes into the industry, according to N., a garment worker in Tangbu West village.
“No one will train anyone here,” N. said. “Even if someone did, it takes six months to get the hang of it, and a beginner wouldn’t make enough to live on.”
Factories take some apprentices on three-to-six-month training programs, but these opening usually require personal connections. And even then, they offer no wage, only meal vouchers.
Some skills are passed down within families.
Factories double as childcare spaces during school holidays, with teenagers learning to use sewing machines, despite notices warning that child labor is against the law.
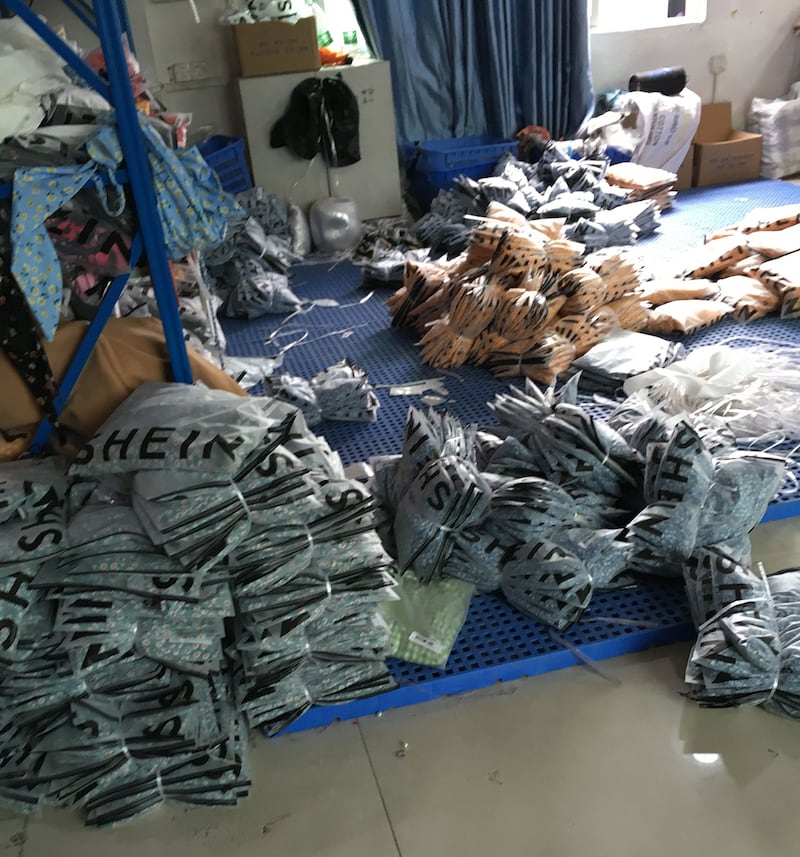
A father working alongside his 15-year-old son told WHYNOT: “If study isn’t an option, learning to sew is a good trade.”
Yet the industry holds fading appeal for the younger generation, given the long hours and physically demanding work.
SHEIN’s influence
E-commerce giant SHEIN is omnipresent in Guangzhou’s garment factories. In Dashi, every two or three workshops have stacks of SHEIN plastic bags piled up; in Tangbu, more than half of the factories supply the company.
In Yuangang, nearly every factory is part of SHEIN’s supply chain.
The company’s fast payment cycle — every two weeks — is a major draw for factory owners.
Job seekers also see the company, which hires through a subsidiary, Zhuotian Business, as a guarantee of stable orders and timely pay.
But the company’s growing influence is also reshaping the industry.
Orders are smaller, styles change faster, and production is more complex.
A 40-something factory worker in Nancun told WHYNOT: “Rates are dropping, and many have quit. Work gets outsourced to Jiangxi, Guangxi and Hunan. What’s left here is the hardest stuff. Maintaining output is a struggle.”
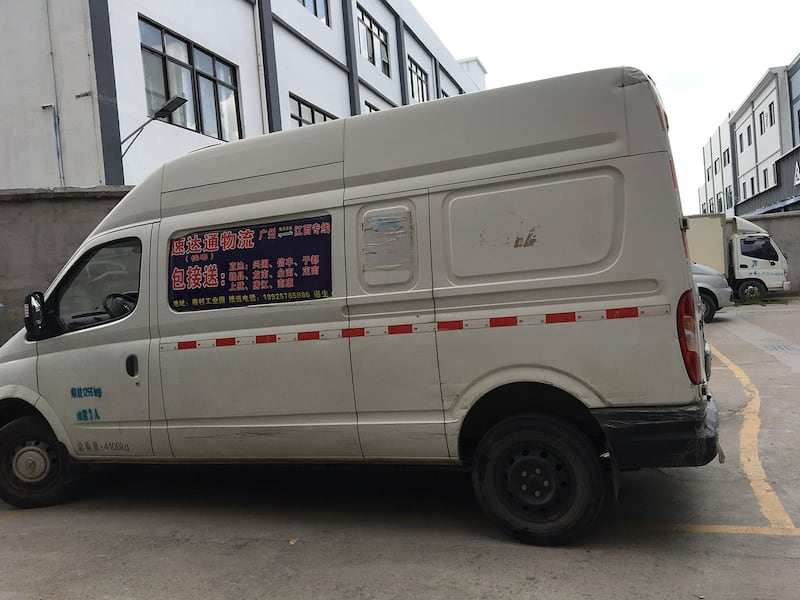
To meet SHEIN’s demand for rapid turnaround times, factories now send fabric pieces to remote processing sites. Vans from Jiangxi or Hunan provinces line the streets, offering daily transport to inland counties where wages are lower.
SHEIN operates a totally digitized supply chain, yet its hiring practices are the same as those of low-cost wholesale garment traders.
SHEIN’s dominance is also drawing scrutiny abroad for quality issues, alleged design theft, and labor conditions.
Factories risk penalties for mistakes — workers in Licun told Wainao they could be fined 300-1,000 yuan (US$40-135) for quality control failures.
SHEIN’s growing control over suppliers raises concerns about whether small factories will face the same pressure as sellers on platforms like Temu, where punitive fines drive businesses to collapse.
Is there a future for Guangzhou’s garment workers?
In urban villages like Nancun, redevelopment plans loom but progress varies. While Lirendong village has seen aggressive demolitions, other areas remain in limbo. Yet workers told Wainao that the most pressing challenge isn’t relocation but income stability.
C., a garment worker in her late 40s with more than 30 years' experience summed up the attitude of this insecure workforce with a shrug.
“We’re migrant workers,” she told WHYNOT. “We go where the work is.”
Translated and edited by Luisetta Mudie. Edited by Malcolm Foster.
歪脑|WHYNOT is a Mandarin-language digital news magazine affiliated with Radio Free Asia